Exploring the Benefits and Innovations of Automotive Plastic Injection Molding
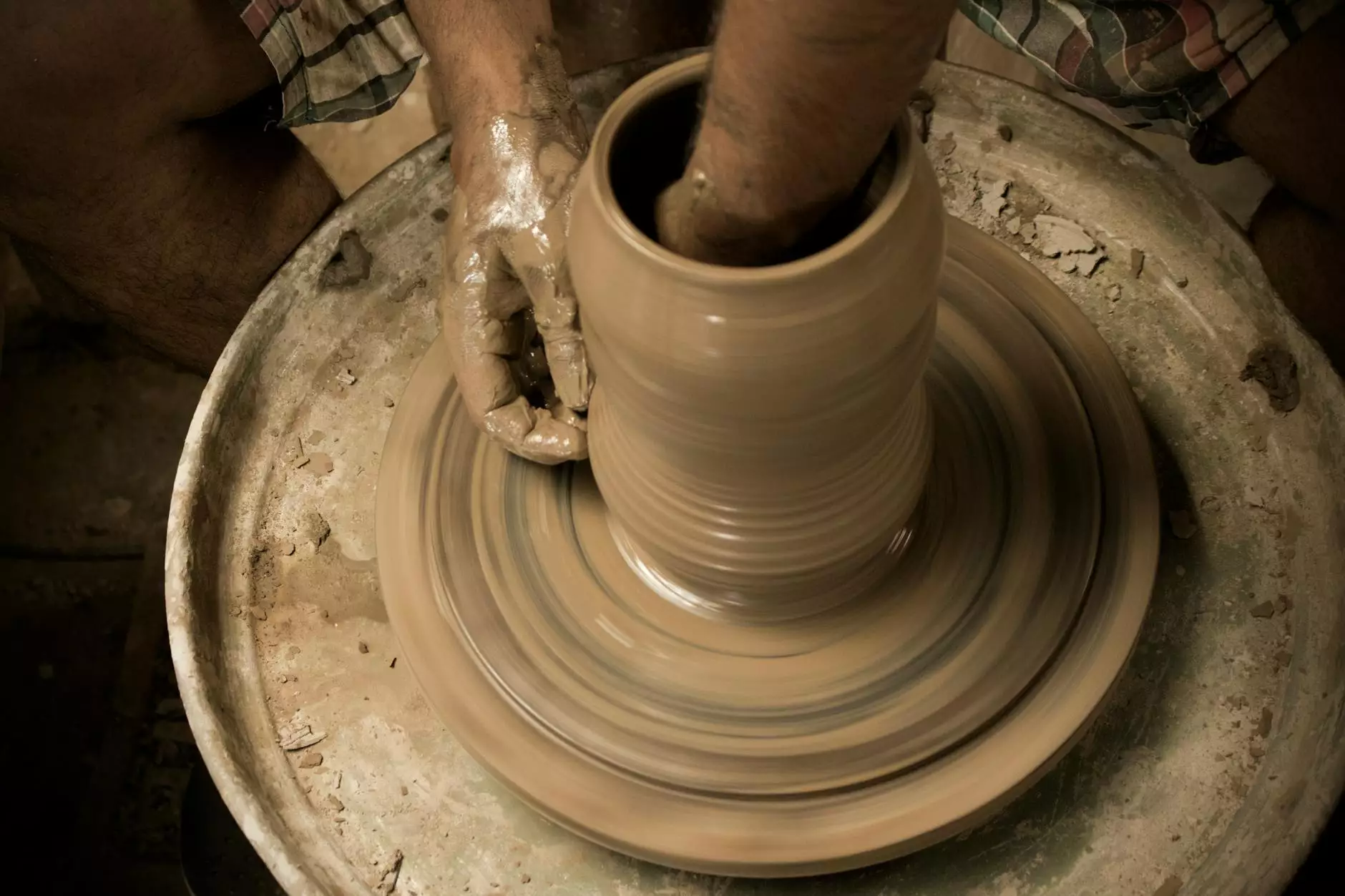
The automotive industry is in constant evolution, driven by the need for efficiency, sustainability, and innovation. One of the key processes that have significantly contributed to these advancements is automotive plastic injection molding. This modern manufacturing method provides unparalleled advantages in terms of design flexibility, cost efficiency, and material properties, making it a cornerstone of contemporary automotive production.
The Evolution of Automotive Manufacturing
Traditionally, automotive manufacturing relied heavily on metals for various components. However, the shift towards plastic injection molding can be attributed to several factors:
- Weight Reduction: Plastic components are significantly lighter than their metal counterparts, contributing to overall vehicle weight reduction and improved fuel efficiency.
- Design Flexibility: Plastic allows for intricate designs that can enhance aesthetic appeal and functionality.
- Cost Efficiency: Lower material costs, reduced machining time, and minimized waste enable manufacturers to save considerably on production.
What is Automotive Plastic Injection Molding?
Automotive plastic injection molding is a manufacturing process where molten plastic is injected into a mold to create complex shapes designed specifically for the automotive sector. This process serves multiple applications including:
- Interior Components: Dashboard panels, center consoles, and door trim pieces.
- Exterior Parts: Bumpers, grilles, and light covers.
- Functional Components: Clips, fasteners, and housing for electronic devices.
The Process of Automotive Plastic Injection Molding
The process of automotive plastic injection molding can be broken down into several key steps:
- Material Selection: Choosing the right type of plastic based on the component's requirements such as strength, temperature resistance, and flexibility.
- Mold Design: Creating a mold that will shape the molten plastic into the desired component. Advanced CAD software is typically used for precision.
- Injection: The molten plastic is injected into the mold under high pressure.
- Cooling: The injected material cools and solidifies, taking the shape of the mold.
- De-Molding: Once the component is cooled, the mold is opened, and the part is carefully removed.
Advantages of Automotive Plastic Injection Molding
The benefits of using automotive plastic injection molding in the automotive industry are numerous, including:
1. Reduced Weight and Increased Fuel Efficiency
As vehicles strive to meet stringent emission regulations, weight reduction has become paramount. Plastic components weigh considerably less than metals, reducing the overall vehicle weight and consequently improving fuel efficiency.
2. Cost-Effectiveness
Plastic injection molding can produce parts in high volumes with minimal waste, making it a cost-effective solution for automotive manufacturing. This efficiency translates to lower manufacturing costs, which can be passed on to consumers.
3. Design Versatility
Plastic's moldability allows for complex shapes and designs that would be impossible or expensive to achieve with metal. This flexibility empowers automotive designers to innovate freely without being limited by material constraints.
4. Durability and Corrosion Resistance
Modern plastics used in injection molding offer remarkable durability and resistance to harsh environmental conditions, making them ideal for automotive applications where exposure to moisture, heat, and chemicals is common.
5. Sustainability
The automotive industry is increasingly focused on sustainable practices. Many plastics used in injection molding can be recycled, and advancements in biodegradable plastics are paving the way for eco-friendlier options.
Trends Shaping the Future of Automotive Plastic Injection Molding
As technology advances, so does the field of automotive plastic injection molding. Several trends are shaping its future:
1. 3D Printing Integration
3D printing technology is increasingly being utilized in conjunction with traditional injection molding. This integration allows for rapid prototyping and innovative designs before final production.
2. Smart Materials
Advancements in materials science have led to the development of smart materials, which can respond to environmental changes or operational conditions, enhancing functionality and safety in automotive applications.
3. Increased Use of Recycled Plastics
With a growing focus on sustainability, manufacturers are increasingly using recycled materials in the production of automotive components, reducing environmental impact and meeting consumer demand for eco-friendly options.
4. Automation and Robotics
Automation is revolutionizing the manufacturing process. Automated systems help enhance production speed, reduce human error, and improve overall precision in automotive plastic injection molding.
5. Lightweight Composites
The marriage of plastics with fibers such as carbon and glass is producing lightweight composites that bring added strength and performance to automotive applications.
Real-World Applications of Automotive Plastic Injection Molding
Various companies are leveraging the advantages of automotive plastic injection molding to create innovative solutions:
- Ford: Utilizing advanced plastics for areas like dashboard assemblies to reduce weight while maintaining durability.
- Toyota: Implementing injection molded components in hybrid and electric vehicles for optimal performance and weight management.
- Volkswagen: Innovating with composite plastic materials designed for enhanced strength in safety components.
The Future of Automotive Plastic Injection Molding
Looking ahead, the future of automotive plastic injection molding appears promising. As the automotive industry continues to push for improvements in efficiency, sustainability, and design, we can expect:
- Greater Innovation: Continuous advances in technology will lead to new materials and processes that enhance the performance and capabilities of automotive components.
- Stronger Regulations: The push for eco-friendly materials will lead manufacturers to prioritize recycling and sustainable sourcing.
- Enhanced Consumer Engagement: With an increasing number of features integrated into vehicles, manufacturers will need to focus on consumer needs for functionality and aesthetics.
Conclusion
In conclusion, automotive plastic injection molding has transformed the automotive industry by providing numerous benefits, including weight reduction, cost effectiveness, design versatility, durability, and sustainability. As we move towards a future driven by innovation and sustainability, the role of plastic injection molding will only grow. As automotive manufacturers embrace these advancements, they will inevitably enhance consumer satisfaction and engagement, ensuring that the industry remains at the forefront of technology and environmental stewardship.
For businesses looking to leverage automotive plastic injection molding for their manufacturing needs, partnering with experts in the field—such as DeepMould—will ensure access to cutting-edge solutions and innovations that can help stay ahead in a competitive market.